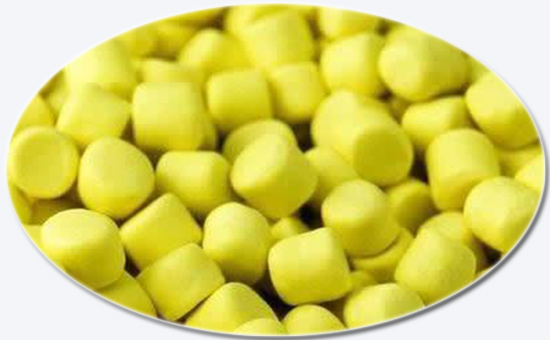
硫磺是橡胶制品加工过程中最传统的硫化剂,在硫磺的作用下,橡胶线性大分子会转变为三维网状结构,橡胶由“生”变“熟”,赋予胶料弹性、耐热性、拉伸强度等;使用再生胶生产橡胶制品时,硫磺同样是最常用的硫化剂,尤其是生产一些高强力高耐磨橡胶制品时。实际上,硫磺在胶料中难分散、易焦烧,因此混炼时需要严格控制硫磺添加方法与添加时机。
1.注意硫磺添加温度
硫磺本身熔点低,在100℃左右的温度下就会发生液化、结团问题,因此在混炼过程中加入硫磺时,混炼温度必须控制在100℃以下,避免混炼温度过高、硫磺的液化结团问题导致胶料混炼不均、硫化时局部焦烧等问题出现,提高再生胶混炼均匀程度,保证再生胶制品质量。
2.注意硫磺添加时间
再生胶选择硫磺硫化时,通常在混炼的最后阶段迅速加入硫磺,这样可以有效避免焦烧。需要注意的是,丁腈橡胶与再生胶并用生产橡胶制品时,由于硫磺1JLYY1210在丁腈胶料中的溶解度小,很难均匀分散,因此需要在混炼初期加入硫磺;为避免焦烧,硫化促进剂放在最后加入即可。
3.注意硫磺添加方式
硫磺是典型的粉状配合剂,在添加过程中很容易根据“风向”因素飞扬,导致硫磺无法在胶料中均匀分散,因此再生胶混炼过程中,硫磺可以与hb软化油、石蜡、陶土、碳酸镁等配合剂共同制成膏状物加入,或制成母胶,避免硫磺在加入过程中出现“乱飞”的问题。
再生胶是废旧橡胶制品回收再加工的产物,在生产过程中经历了脱硫工序,但本身还会含有一定量未被完全祛除的促进剂等,这时设计含再生胶制品配方时,需要将这部分配合剂用量计算进去,合理调整硫磺用量,避免欠硫、过硫等问题出现;在再生胶混炼过程中严格掌握硫磺的添加时机,为后续硫化等操作提供更好的条件,进一步优化再生胶制品综合指标。
独家原创文章【商业授权】无书面授权禁止任何形式转载,摘抄、节选。关注鸿运橡胶:学习再生橡胶生产橡胶制品的工艺配方和原料的技术,帮您降低成本增加利润。