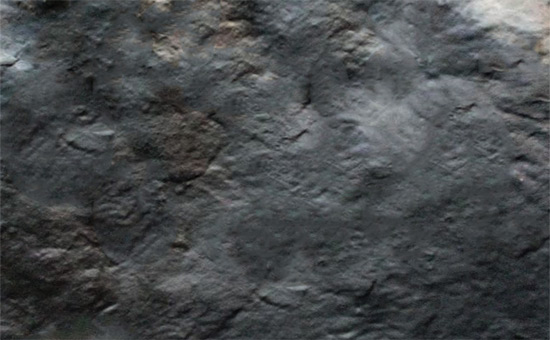
焦烧是胶料在存放和加工过程中由于热量积累产生的早期硫化现象,导致橡胶制品表面不光亮、有皱纹、表面不平,且材质变脆易裂。焦烧的主要原因是硫化体系选择不当或硫化剂、促进剂用量不合理。以再生胶为主要原料生产橡胶制品时,合理设计硫化体系,提高再生橡胶的焦烧安全性至关重要,尤其是在生产过程中需要长时间加工的再生橡胶制品。
1. 注意再生胶硫化剂与促进剂的配合
再生胶制品硫化配方中,选择在加工温度下反应速度较慢的硫化剂,严格控制硫化剂的用量,避免过量使用导致过早焦烧。优先配合迟效性或临界温度较高的促进剂;合理搭配促进剂和活化剂(如氧化锌、硬脂酸等),以达到最佳的硫化效果和焦烧性能。
2. 硫化促进剂选择要点与焦烧性能
提高再生胶焦烧安全性需要在选择促进剂时优先考虑硫化促进剂的焦烧性能。建议选择含有防焦官能团(-SS-)和辅助防焦基团(羰基、羧基、磺酰基、磷酰基、硫代磷酰基、苯并噻唑基)的促进剂E4LYY124。比如,次磺酰胺类促进剂焦烧时间长、硫化速度快、硫化曲线平坦、综合性能较好,加工安全性好,适用于再生胶厚制品硫化。
各种促进剂的焦烧时间依下列顺序递增:ZDC < TMTD < M < DM < CZ < NS < NOBS < DZ。在实际应用中,再生胶制品可以采用几种类型促进剂并用的体系,以达到最佳的硫化性质和加工安全性。
3. 促进剂并用 提高再生胶焦烧安全性
(1)使用秋兰姆类促进剂硫化的再生胶胶料配方,减少秋兰姆促进剂用量,并与次磺酰胺类或噻唑类促进剂并用,可以延长焦烧时间。
举个例子:促进剂TMTD硫化诱导期短,可使胶料快速硫化,当TMTD作为主促进剂使用时,与次磺酰胺类或噻唑类促进剂并用,可以延长焦烧时间;避免将促进剂TMTD与促进剂D或二硫代氨基甲酸盐并用,否则会降低再生胶胶料的耐焦烧性。
(2)胍类促进剂热稳定性高,比如促进剂D,作为主促进剂,胶料焦烧时间长,硫化速度慢。
(3)天然橡胶/再生胶并用生产橡胶制品时,噻唑类和次磺酰胺类促进剂与DTDM配合可以提高胶料抗焦烧性。
(4)丁基橡胶、丁基再生胶制品硫化体系中选择二硫代氨基甲酸盐类促进剂,对焦烧安全性更有利。含有促进剂TMTD和氧化锌的氯化丁基橡胶、氯化丁基再生胶胶料中配合使用氧化镁或促进剂DM,可以延长胶料焦烧时间。
再生胶制品生产中合理选择硫化剂、促进剂的品种,严格控制其用量,可以有效提高再生胶焦烧安全性。在实际生产中,补强剂、填充剂、软化剂品种,再生胶硫化条件等都会影响焦烧安全性,后续继续与您讨论相关问题。
独家原创文章【商业授权】无书面授权禁止任何形式转载,摘抄、节选。关注鸿运橡胶:学习再生橡胶生产橡胶制品的工艺配方和原料的技术,帮您降低成本增加利润。