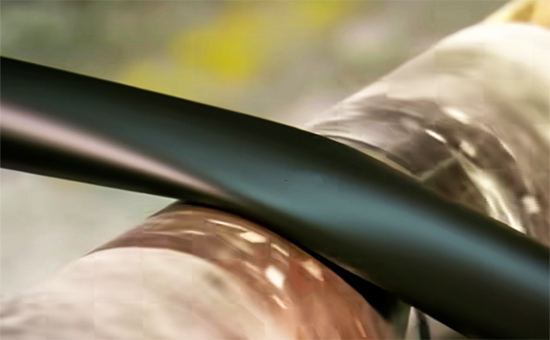
丁基再生胶具备优异的气密性、水密性,可单独使用或与丁基橡胶并用生产汽车、摩托车、自行车内胎产品,有效降低橡胶内胎原料成本。丁基橡胶、丁基再生胶或丁基橡胶/再生胶并用胶制备丁基橡胶内胎时,挤出工艺至关重要,本文主要与您分享丁基橡胶内胎挤出工艺注意事项。
1.注意热炼温度与辊距
使用丁基橡胶、丁基再生胶或丁基橡胶/再生胶并用胶制备橡胶内胎时,丁基胶料建议采用低温热炼,在冷辊条件下小辊距充分精炼;前辊温度应控制在45-55℃,后辊温度在50-60℃之间,有助于胶料在前辊上形成良好的包辊状态,同时避免过度的分子链松弛;更好地保持胶料的弹性状态。
2.注意滤胶工艺操作温度
滤胶是确保丁基橡胶内胎质量的关键步骤。供胶条温度需控制在80℃以下,机身温度为50±5℃,机头温度为70±5℃;滤胶后胶温不得超过135℃。使用28目和40目滤网各一层,以确保丁基胶料的均匀性和纯净度。
3.注意加硫黄时机与加硫黄后的工艺操作
丁基橡胶、丁基再生胶、丁基橡胶/再生胶并用胶生产橡胶内胎时多使用硫黄-促进剂体系,加硫黄工艺对产品质量有显著影响。硫黄的添加时间有两种,滤胶后加硫黄和先加硫黄后滤胶。
(1)滤胶后加硫黄:建议在冷辊下加入硫黄和超促进剂比如TMTD;首先胶料散热,后抽出余胶,加硫黄和超促进剂,吃净后经过3-4次薄通,2-3个三角包,捣炼后下片,整个操作过程约10分钟;胶料停放待挤出。
(2)先加硫黄后滤胶:丁基橡胶互溶性和分散性差,硫黄分散不均容易出现硫黄斑点,造成挤出后分层、砂眼等质量问题;与丁基橡胶相比,丁基再生胶E4LYY129的相容性、分散性更好。先加硫黄后滤胶可以更好地保证半成品质量;滤胶时各段温度均比先滤胶后加硫黄的挤出工艺降低5-10℃,滤胶后胶温不能超过105-125℃,避免焦烧;此时滤胶后不需要进行停放,直接精炼,供挤出机挤出即可。
生产丁基橡胶内胎时,丁基胶料挤出前需在低温下精炼,此时需要注意螺杆转速,胶筒挤出后必须停放4小时后再使用。以丁基橡胶、丁基再生胶为主要原料生产橡胶内胎时,橡胶制品厂家还需要合理确定丁基再生胶的掺用比例,适当调整生产配方以及各个生产工艺工序,后续继续与您讨论丁基橡胶内胎降低成本的技巧以及生产工艺要点。
独家原创文章【商业授权】无书面授权禁止任何形式转载,摘抄、节选。独家原创文章【商业授权】无书面授权禁止任何形式转载,摘抄、节选。关注鸿运橡胶:学习再生橡胶生产橡胶制品的工艺配方和原料的技术,帮您降低成本增加利润。