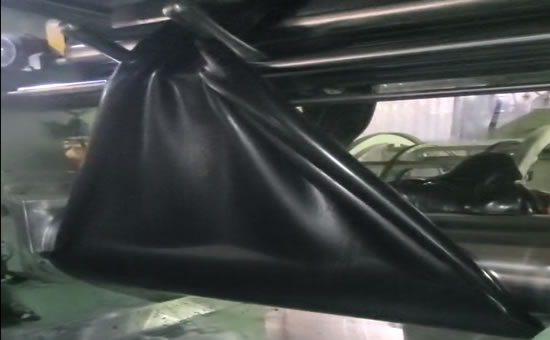
轮胎再生橡胶具有橡胶烃含量高、弹性好、机械强度大,可与天然橡胶、丁苯橡胶等并用等特点,被广泛应用于多种橡胶制品中降低原料成本。部分新朋友没有使用过轮胎再生胶,或者以前用乙丙橡胶、丁腈橡胶的朋友第一次接触轮胎再生胶,在使用过程中的第一个问题就是塑炼与混炼如何做的问题。今天小编与您探讨轮胎再生胶需不需要塑炼以及混炼时需要注意的问题。
首先说塑炼,塑炼的意义在于使橡胶达到合适的可塑度。如果橡胶达不到所需的可塑度,会给混炼带来很大的困难(发生脱辊等现象)橡胶的收缩率增大;如果橡胶过度塑炼,会造成橡胶的硬度、拉伸强度降低,耐老化性能下降等。为了保证后续工序的顺利进行,必须对橡胶进行塑炼加工。一般模压型橡胶制品要求可塑度在0.3左右,压延、挤出、海绵发泡料的可塑度要求在0.5左右。塑炼并非是橡胶加工的必备环节,需要根据橡胶原材料的塑炼特性、门尼粘度等综合判定,一般门尼粘度(ML100℃ 1+4)在80以下胶料可不必进行塑炼(特殊用途或性能除外)。轮胎再生橡胶门尼粘度(ML100℃ 1+4)一般在60左右,混炼前在密炼机直接混合增塑剂、填充剂等即可,也可直接开炼机薄通几次后进行混炼,所以轮胎再生胶大多不需要经过塑炼工艺的,这也是轮胎再生胶比天然橡胶能降低工电费成本的原因。
使用密炼机的朋友,请拿好手中的硫化剂、促进剂、防老剂、氧化锌等产品,提早加进去叠加密炼机温度控制不到位,还没有排胶可能胶料已经半熟或者全熟了,这取决于密炼时间和温度,相当于不用硫化机提前进行了无加压硫化过程。
然后说说混炼,轮胎再生胶经过密炼机加入炭黑、增塑剂、填充剂后开炼机(自动翻胶机略有不同)混炼过程中需要注意以下三点:
1、各种配合剂要充分混炼均匀,严格过辊遍数和打三角包,否则会引起胶料焦烧或硫化不熟。
2、要严格按照混炼胶工艺加料顺序进行混炼,不可随意更改顺序或者一股脑全部加进去。
3、为了保证混炼胶的可塑度,混炼时间要严格掌握。
做到以上几点,熟练使用轮胎再生橡胶降低成本就变成了很简单的事情。如果您遇到过塑炼或者混炼工艺方面的问题,欢迎留言给我们进行探讨;如果您有更好的塑炼、混炼方面的方法,也请您与我分享,帮助更多的朋友在保证制品质量的前提下降低成本。
独家原创文章【商业授权】无书面授权禁止任何形式转载,摘抄、节选。关注鸿运橡胶:学习再生橡胶生产橡胶制品的工艺配方和原料的技术,帮您降低成本增加利润。